
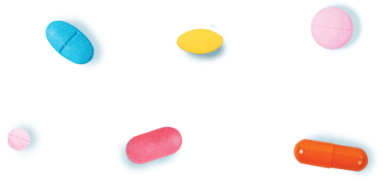
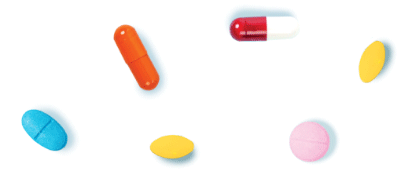
For decades, development of production facilities has been driven by stringent requirements for cleanliness and consistency, resulting in plants that often cost at least $1 billion and are designed to produce only a few products. Past philosophies leaned toward conservative, robust design to combat the lack of technology in equipment and lessen the impact of the significant human interaction with the process.
The 2008 recession in the U.S. prompted the beginning of an industry shift. With less capital available, facilities needed to cost less to build and maintain — and the quickest path to reducing cost was to reduce the exposed environment. Improvements in technology and equipment also allowed manufacturers to reduce the amount of aseptic, or clean, space needed to produce drugs.
“This small change created a ripple effect in the built environment, lessening the requirements for HVAC, electrical and other support utilities — and it worked,” Yount says. “Drugs could be produced less expensively and more safely. But facilities were still highly segregated, with only about 20% of space devoted to where the product was actually processed.”
With the advent of personalized medicine, it’s not sustainable to divide a manufacturing space according to those proportions.
A Personal Perspective on Personalized Medicine
“In the years I’ve spent supporting the built environment for pharmaceuticals, I’ve been exposed to many points of view,” says Amber Yount, pharmaceutical department manager at Burns & McDonnell. “As a consultant, I know companies spend billions of dollars developing drugs, testing them for safety and efficacy, and creating a repeatable manufacturing process that ensures quality. As a mom, I know there are trust issues between society, drug companies and the governmental agencies that oversee them. As a friend of someone fighting cancer, I know drug development and approval often takes too long and doesn’t address the patient holistically. And as an American, I worry about the social implications of personalization on rising drug costs. As an engineer, though, I know there is a solution to the challenges we face. To say that it’s complicated is a gross understatement, but with a strategic, forward-thinking approach and a personal commitment to finding success for clients and patients, we can find it.”
A Custom-Built Future
Personalized medicine lacks many of the current economies of scale associated with today’s large-scale manufacturing processes. As drugs are customized to genetic sequence and DNA, their number and diversity will radically increase. Large-batch production will give way to small-volume processes.
The built environment must both meet today’s needs and be nimble enough to address a completely different future.
“Keeping pace with the fast-moving drug development process will require more agile and flexible systems that can maintain quality and safety standards for several different products,” Yount says. This future will likely encompass a number of considerations.
Enclosing Production
Shrinking the size of the enclosure around the product minimizes the requirements for aseptic space devoted to production. “The surrounding environment can then be shared to create flexibility, improve ergonomics and reduce building costs without compromising the safety of the product,” Yount says.
Containerization
When the number of doses is 10 instead of 10 million, manufacturing will be completed in a box instead of a ballroom. A tabletop, container-based approach is more flexible, movable and local. With a production space the size of a shipping container, could many of these be stacked several high along rows in a warehouse‑type facility? Could materials be delivered to and taken from these containers via an automated storage and retrieval system? Both are possible scenarios.
Shared Infrastructure
Instead of sinking costs into buildings, storage, data integrity and logistics, pharmaceutical companies could lease space from a developer alongside other companies. Utilities and infrastructure would be shared and metered, recapturing some economies of scale lost with personalization. Data could be stored and secured in the cloud.
Disposability
Many of today’s drugs are manufactured in massive, stainless steel components that are costly to create and clean. When the end product is just a few personalized doses instead of millions of vials, the components might not need to be as robust. Advances in single‑use, disposable materials could mean a manufacturing process where the components are small, inexpensive, aseptic, cleanable and sustainable.
Design for Now
The specifics of precision medicine are redefined in the healthcare industry on a daily basis, so flexibility and innovation are vital. An initial focus on the building envelope can help companies anticipate change to better serve their end users.
“Maximize column spacing and roof height, provide a roof structure that can support pipe racks for utilities, and supply foundations and slabs that can support large live and dead loads,” Yount says. “In other words, build a nice warehouse or have someone build it for you to lease, then fit it out as modularly and flexibly as possible.”
A more flexible envelope will better enable future customization. And if the shift to a different manufacturing approach is swifter than expected, a warehouse-like space always has value in the market.
Yount also suggests looking to other industries for insight.
“Designing in a pharma-only vacuum can lead to complacency,” she says. “Looking at how others
solve problems can inspire a fresh approach.”
For example, instead of installing a farm of lab-scale freezers — then building the necessary supporting infrastructure to offset the heat it produces — a facility might benefit from the hot aisle/cold aisle approach popular in data centers, whereby cooling costs are cut by aligning racks and other equipment to optimize air flow.
The research, development and manufacturing of pharmaceuticals is a cautious, lengthy process, with companies working hard to meet the needs of stakeholders and patients. The advent of personalized medicine will introduce a momentous shift in the market, making these goals even more challenging. A collaborative, forward-thinking partnership between pharma companies and those who build their manufacturing facilities can help conquer the coming transition.
Want More?
See how real estate knowledge helped a growing manufacturer settle into the right facility.
Read More