The skilled labor force challenge has been building for years, but now it’s hitting a point where it poses a real risk to the success of projects.
Matt Nordhus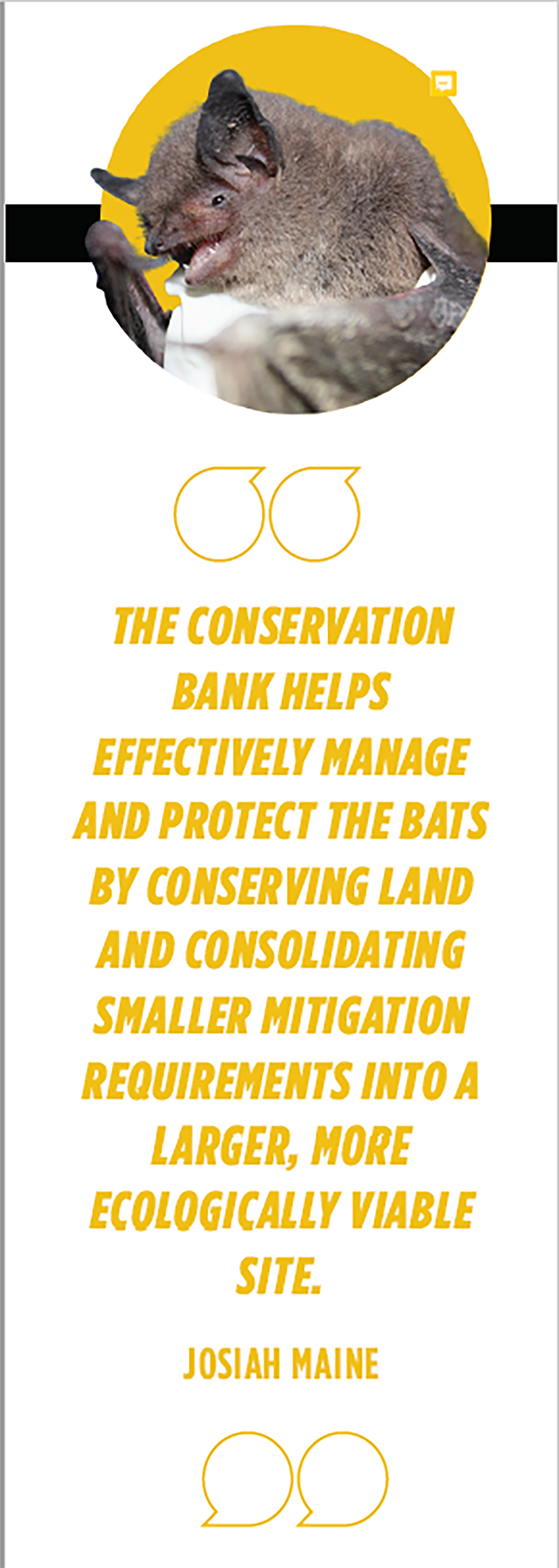
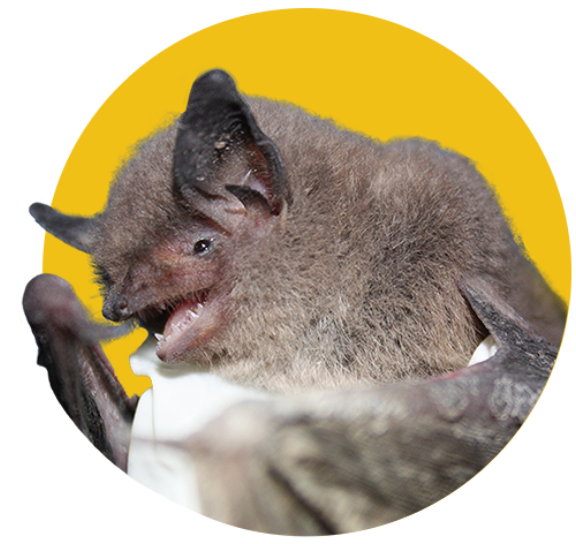

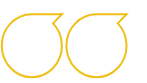
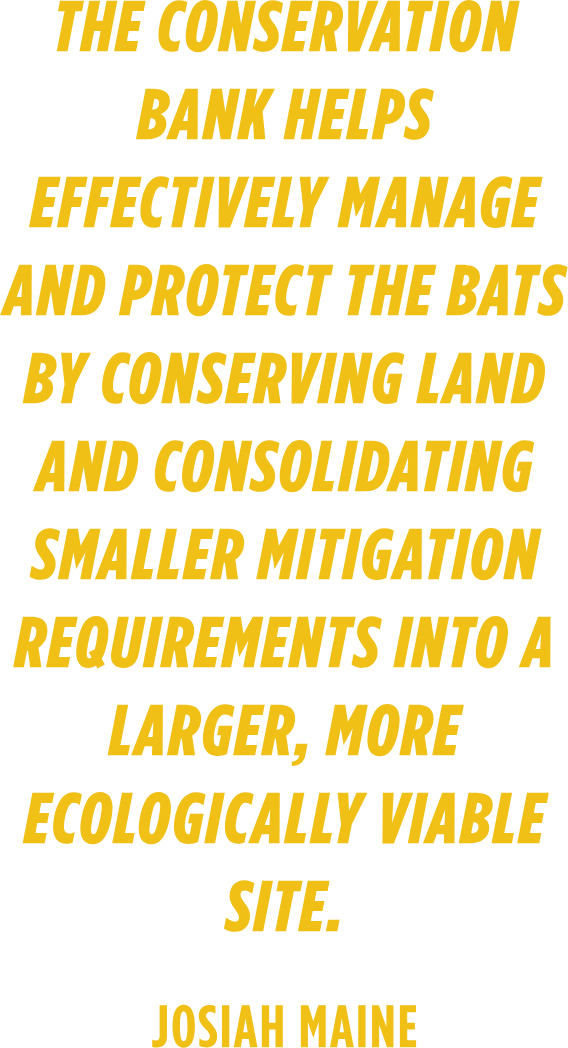
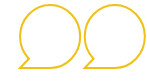
According to a recent survey conducted by Associated General Contractors of America and Autodesk, 80% of the 2,500 respondents reported having difficulty filling hourly craft positions and 56% said filling salaried craft positions was also a challenge. In addition, 81% of firms said that in the short term it would continue to be hard or even get harder to find craftspeople.
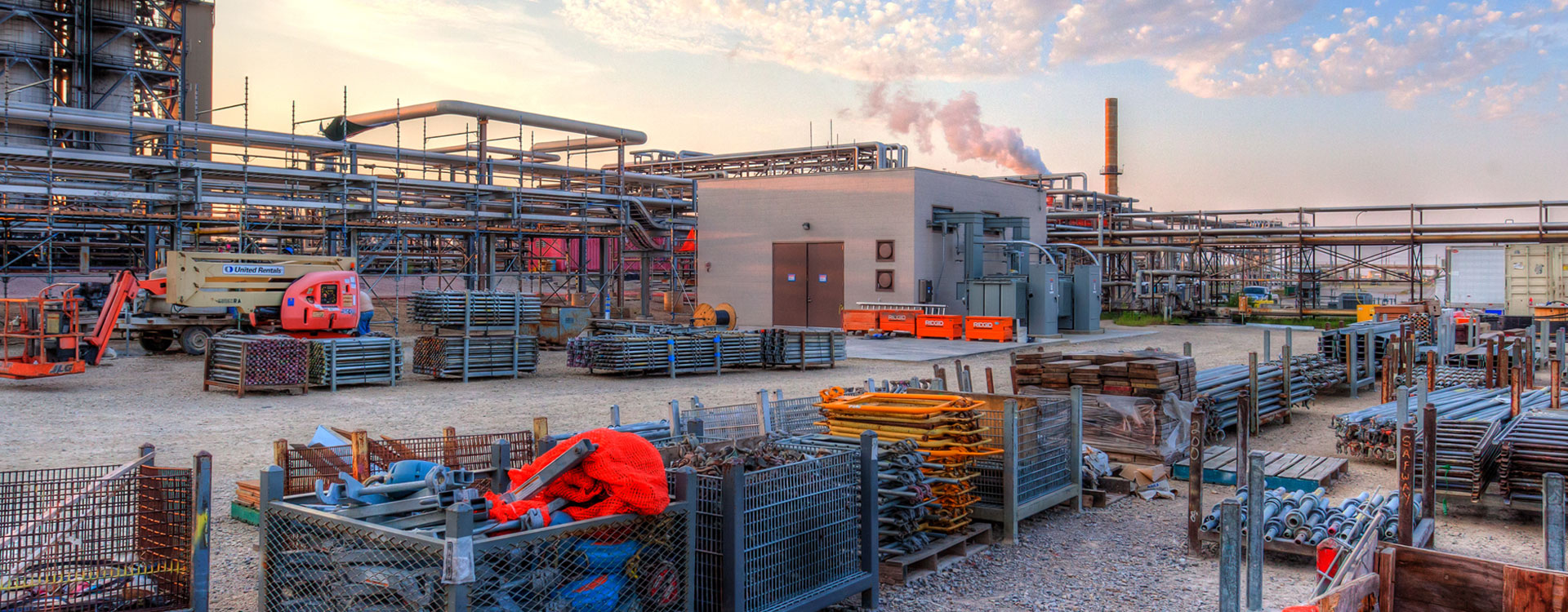
MEGABUILDS STRETCH GULF FOR CRAFT LABOR
With a booming oil, gas and chemicals market, the U.S. Gulf Coast region is feeling a different pinch in the craft labor market than the rest of the U.S. Experienced and qualified workers thrive with strong wages and abundant work; however, the close-knit web of competing projects and the abnormally high ratio of megabuilds have strained the labor market anyway, driving up costs.
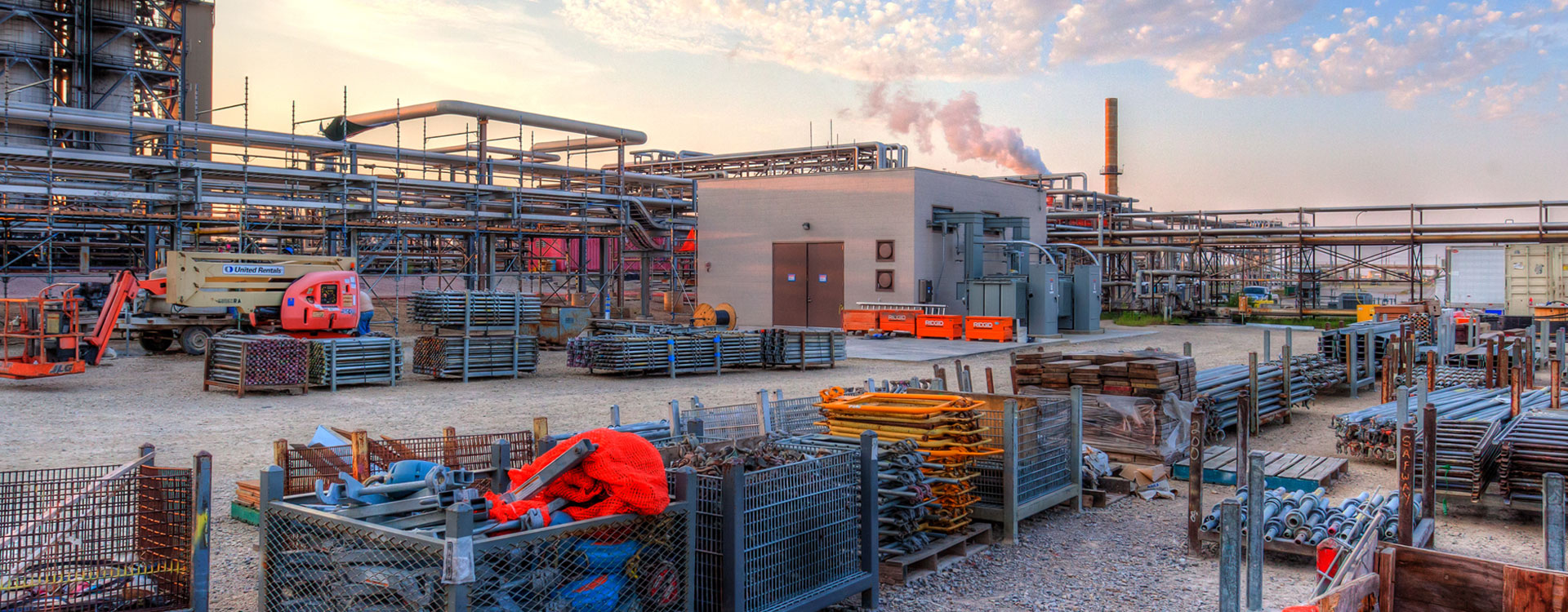
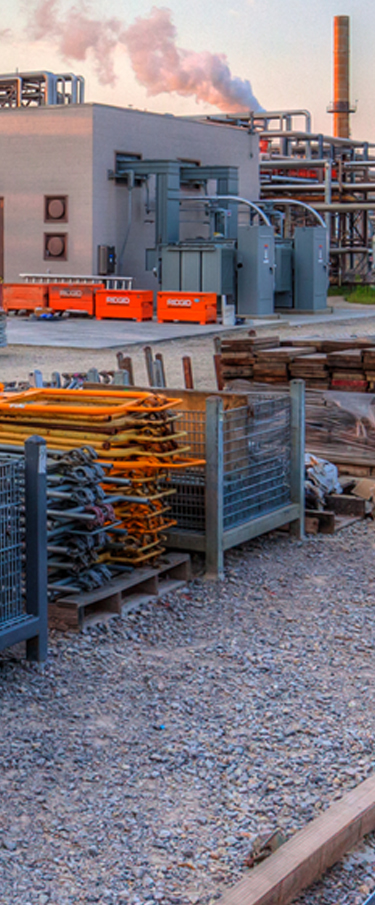
A Unique Outlook in the Gulf
With a booming oil, gas and chemicals market, the U.S. Gulf Coast region is feeling a different pinch in the craft labor market than the rest of the U.S. Experienced and qualified workers thrive with strong wages and abundant work; however, the close-knit web of competing projects and the abnormally high ratio of megabuilds have strained the labor market anyway, driving up costs.
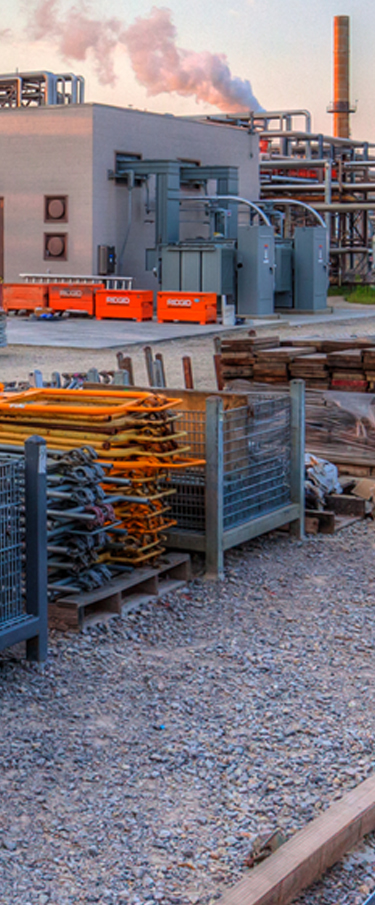
Leaving no industry untouched, the effects of the shortage have affected projects nationwide, straining abilities to complete execution in a timely manner. And in regions booming with opportunities, adjacent projects compete to lure workers to fill spots with increased per diems or completion bonuses.
“I experienced this firsthand on a power plant project in Louisiana back in the early 2000s,” Nordhus says, “when a competing project 3 miles away raised its per diems and travel allowances and we were forced to hike our pay to retain staff. As you exhaust the labor supply in a region, the projects begin poaching each other’s workers.”
Solving for Shortages
Though it might be tempting to see the craft labor shortage as a construction industry issue that the construction industry needs to fix, its ripple effects have no boundaries — and all will have to live with the results. If something is constructed incorrectly, it can take triple the time to repair it, which could wreck a carefully planned schedule and drive up costs. Or, worse yet, it could jeopardize the safety and integrity of the final product.
“This will be something the industry as a whole is dealing with for a long time to come,” says Jeff Allen, a vice president and regional office manager at Burns & McDonnell who focuses on engineer-procure-construct projects and program management throughout the Southwest.
“The construction companies that will make their clients successful over the coming years are going to be the ones that are best able to deal with the shortage and overcome the challenges associated with it.”
One path to overcome the shortage involves approaching each and every project with that challenge in mind, which has borne several solutions.
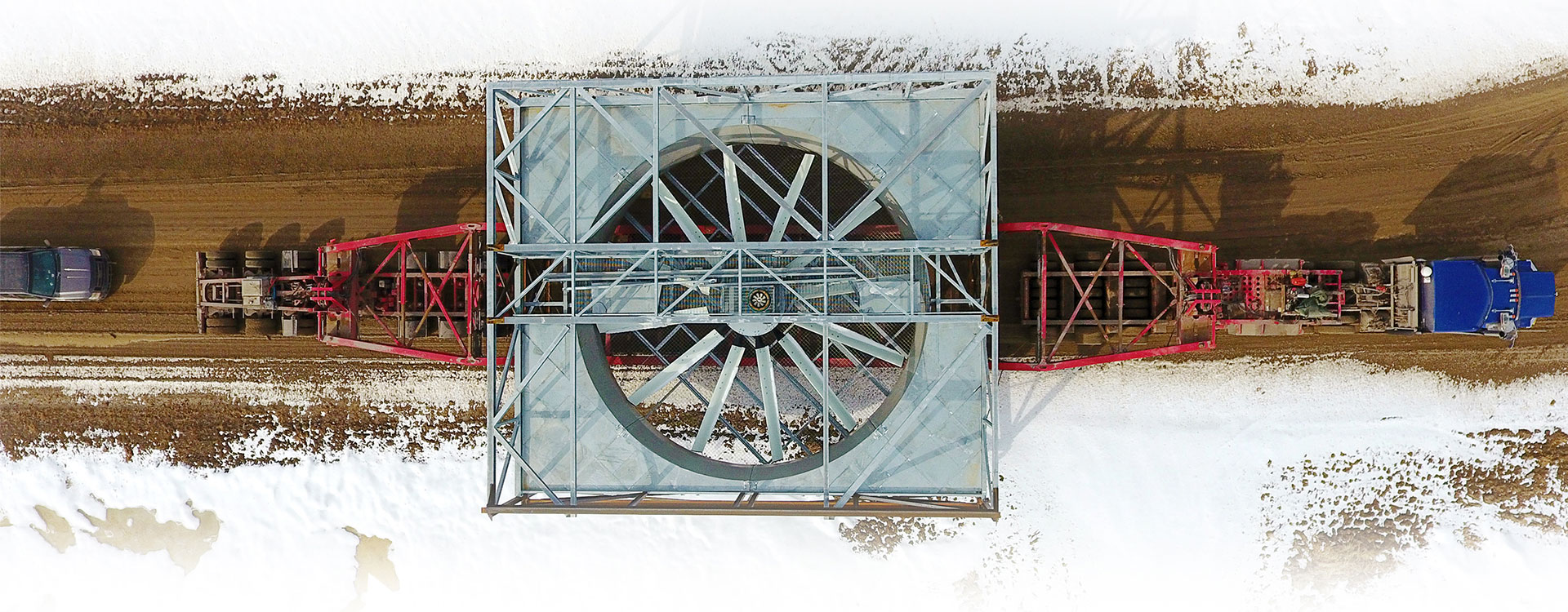
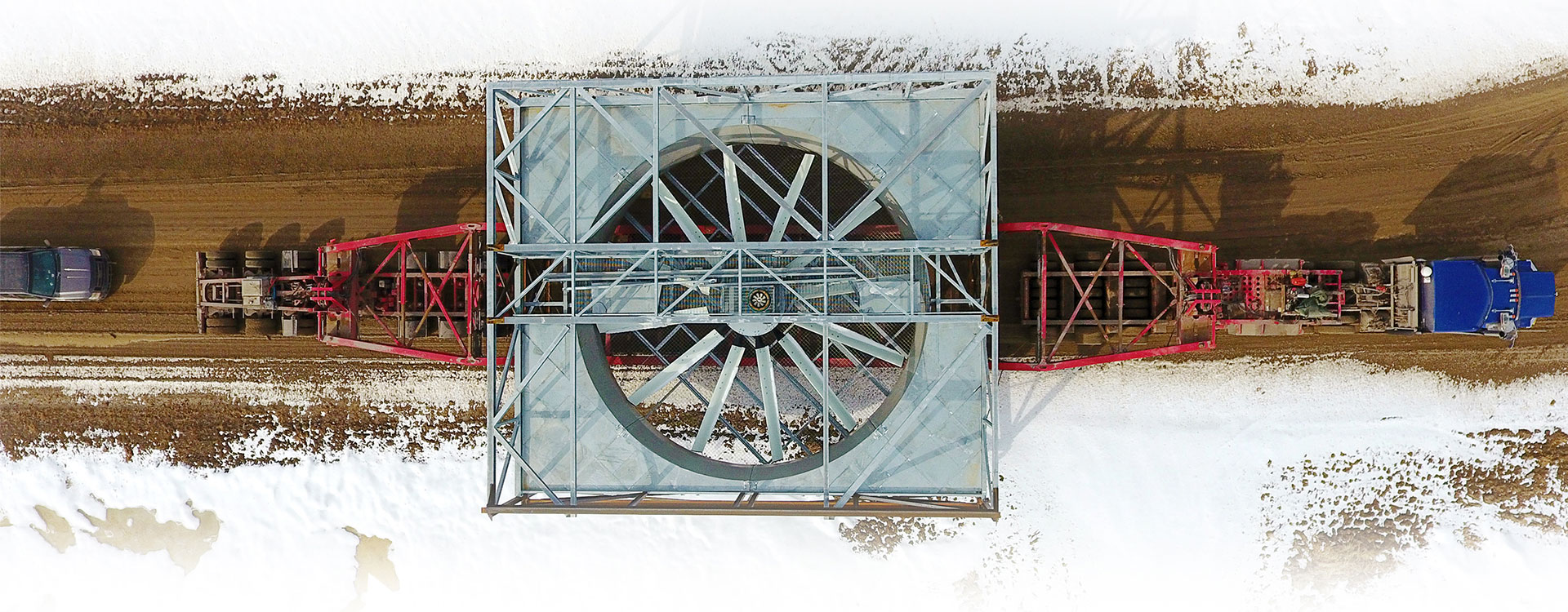
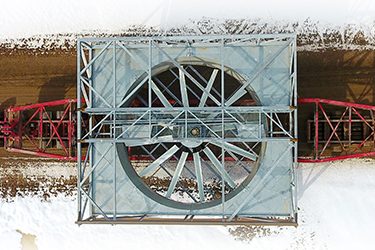
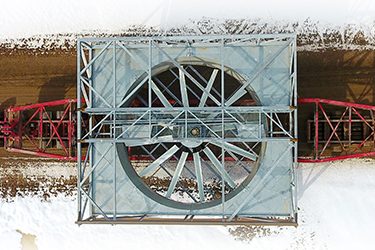
Modularization and Fabrication
The widespread adoption of off-site construction through modularization or fabrication is transforming the construction industry in several markets. With a higher percentage of construction within a structured environment away from the job site, the labor can be more tightly controlled. With this approach in mind, engineers can design specifically for modular components that can be transported to the site when needed.
“It keeps the quantity of tasks down for an individual craftsman,” Allen says, “which increases efficiency, improves safety and allows the training process to be a bit more streamlined.”
Learn more about why prefab is fab here .
Advanced Work Packaging
While every project is unique, performing certain tasks earlier in the project timeline can save time and money, such as prioritizing the development of pipe racks for oil, gas and chemical projects. Known as Advanced Work Packaging (AWP), the process of construction driving the sequence of engineering and procurement deliverables for a project is having a positive impact on schedules and productivity.
“We optimize our engineering and procurement to facilitate starting work earlier,” says Joe Podrebarac, a vice president and construction director at Burns & McDonnell. “This allows us to reduce the total on-site manpower for an extended duration without extending the overall schedule.”
For example, a 12-month project approached traditionally might peak halfway through with 150 craftspeople on-site. However, by identifying scopes of work that could be moved forward in the schedule through AWP, 100 craftspeople could perform the same amount of work but over a longer period of time in the schedule, per the graphic below.
Design Adjustments
Engineering a project design with construction in mind applies to more than shuffling timelines. Actual design decisions can be made to address craft labor constraints by choosing solutions that require substantially fewer people and time. For example, look into incorporating helical steel piles into a design rather than concrete piers because they require less labor. Or, when designing electric transmission poles, select a design shape that is more conducive to flying the line in with helicopters rather than installing manually.
Technology
The use of technology is increasingly being embedded into job sites to help plan and monitor work in the field. Various programs exist to manage the overall progress of work packages as well as give a digital snapshot to track and identify work scope available per week. Combining technology with AWP can build efficiencies in the schedule and reduce congestion of on-site manpower to improve safety performance.
A concerted, team-led effort incorporating one or all of these solutions can help most any project manage the craft labor shortage.
“Will we overcome the shortage?” Podrebarac asks. “Yes, we have to. The projects will get done. The question is if we will be able to overcome it safely, with good quality, while still maintaining good productivity and predictable schedules. That’s our industry’s biggest challenge, and that’s where these solutions come into play.”
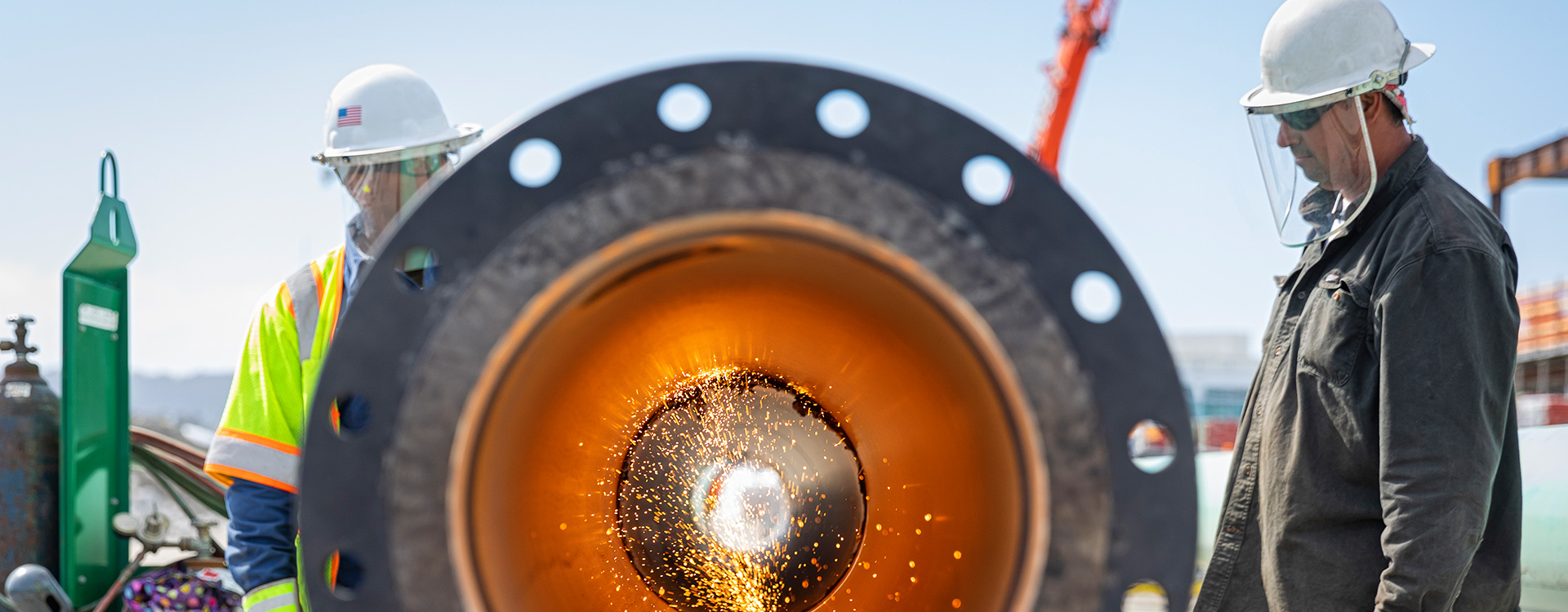
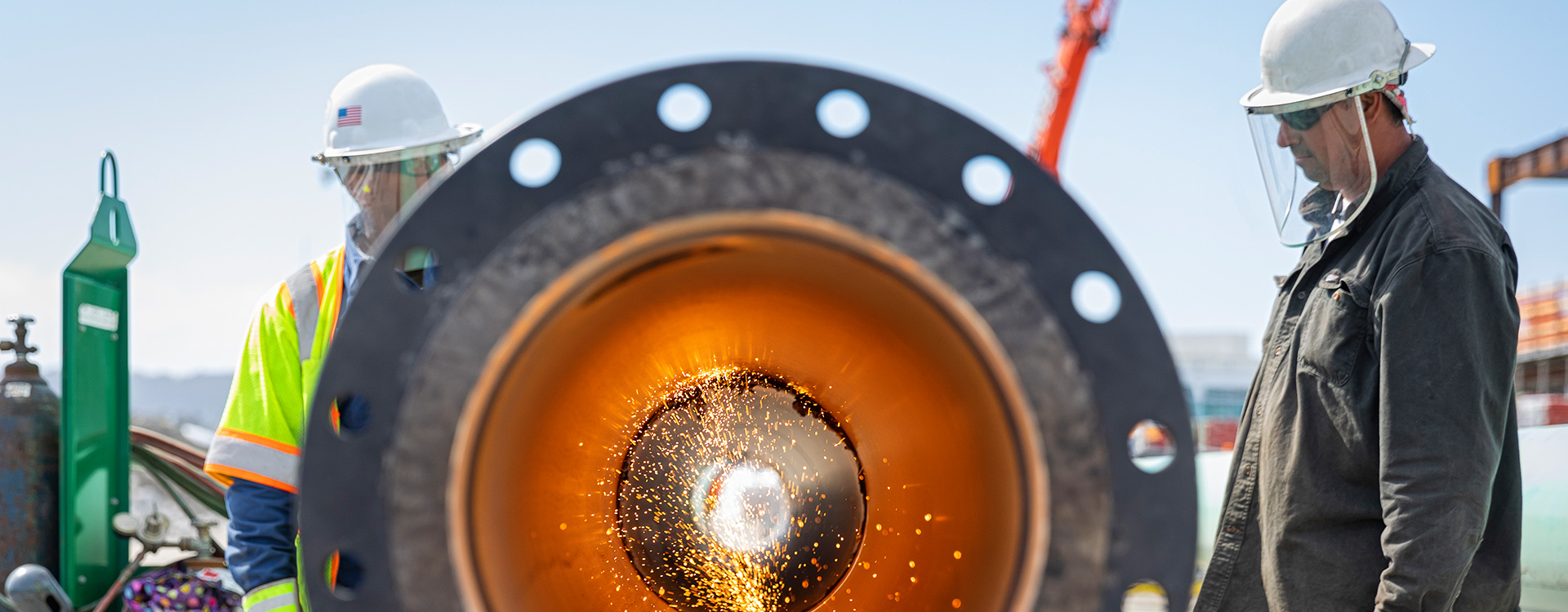
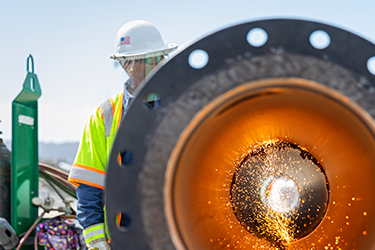
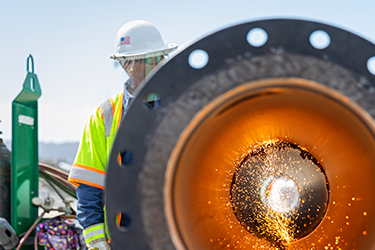
Prepping the Future Pipeline
While these solutions can help maintain safety, quality, timeline and costs for projects in the interim, the industry is still focused on filling the pipeline for future craft workers. Whether organized by unions, private companies or construction-focused organizations, programs and workshops are building awareness among students of all ages across the nation. Specifically, the ACE Mentor Program of America has established a mission to engage, excite and enlighten high school students to pursue careers in design and construction.
Trade schools also are becoming more active in the recruitment of high schoolers.
“There’s a significant focus on encouraging college-bound students to select majors that are construction-focused,” Allen says. “We’re even seeing large construction firms taking an active role in construction science schools across the country.”
Will we overcome the shortage?
Yes, we have to.
These firms are taking the initiative to support the educational activities of these institutions and help students select and stay in construction science-focused degree programs. Some companies also are developing and implementing in-house training programs to fill the experience gap in new workers with on-the-job opportunities on active projects.
“Private firms have a valuable role to play in helping build the craft labor pipeline for the construction industry,” says Renee Gartelos, a vice president and director of human resources at Burns & McDonnell. “We want our construction partners to identify and train talented workers, and together, we can make the biggest impact.”
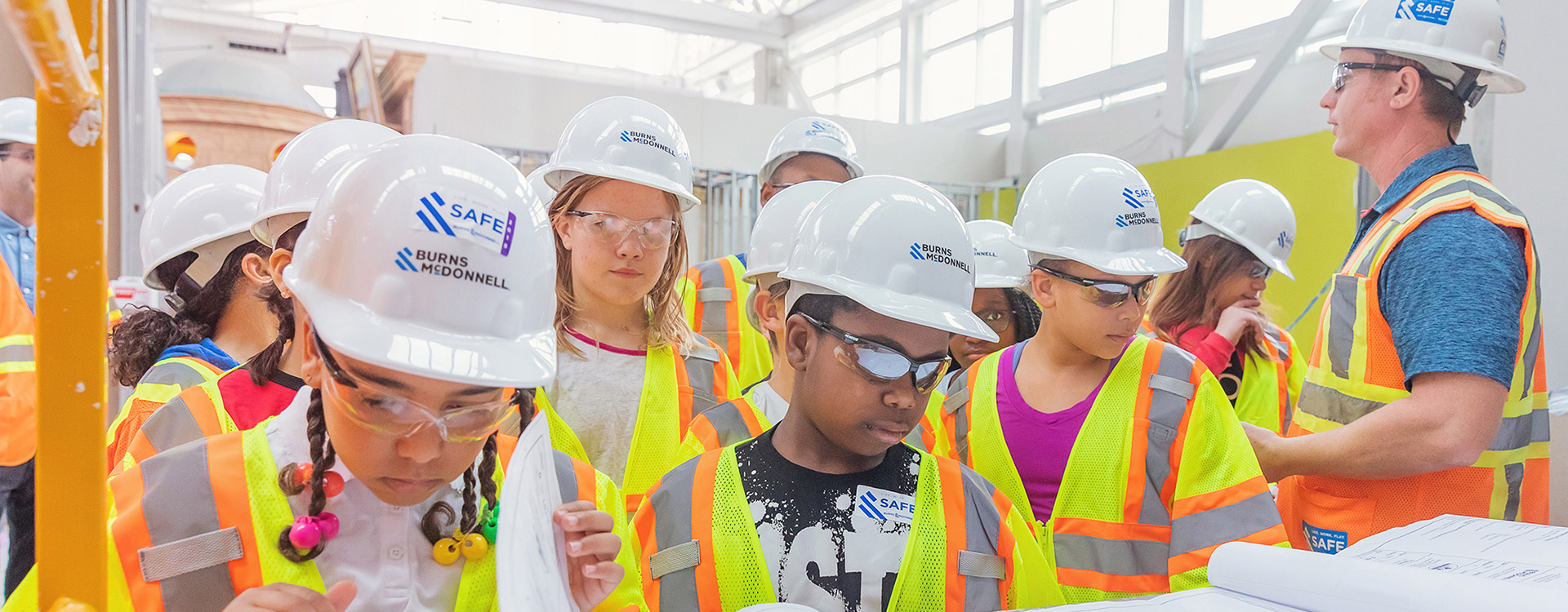
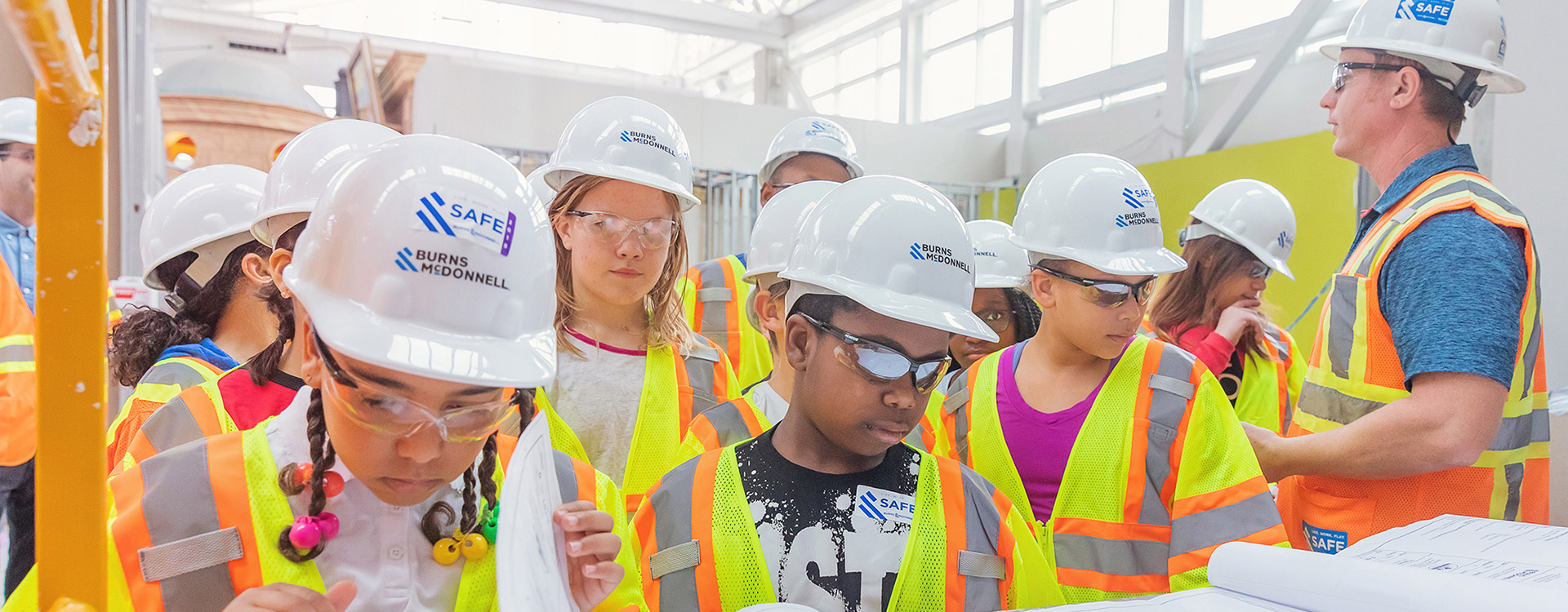
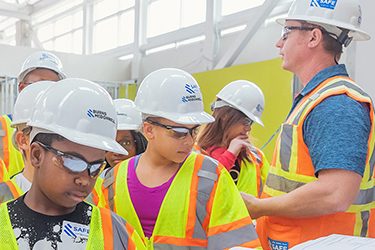
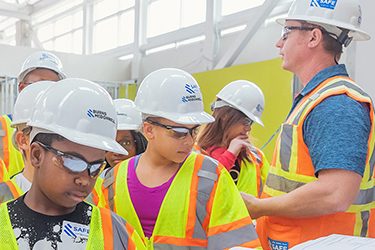
However, these efforts still present ongoing obstacles. Aside from the facts that the work can be hazardous, long-term retention is becoming more uncommon, and often the highest paying opportunities tend to be mobile jobs, the qualities that are expected of new craftspeople are shifting a bit, too.
“Our projects are getting more complex with more technologies in use and are slowly moving toward design-build executions,” Allen says. “The interfaces that construction professionals will face in the future will be multilayered and more complex.”
Building Confidence in Construction
With demands high and the future unknown, it will take collective voices from all industries touching construction to move the needle — a collaboration style that managed to drive interest in science, technology, engineering and math (STEM) careers not that long ago.
“People began talking about STEM and the significance of STEM-related careers, which increased awareness over time,” Gartelos says. “We’ve seen success, so I have confidence that it can be created in the construction space for the long term.”