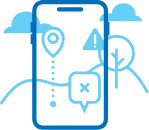
AUGMENTED
REALITY (AR)
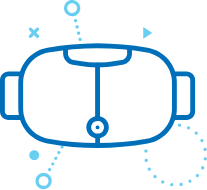
VIRTUAL
REALITY (VR)
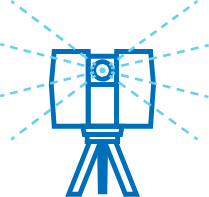
3D SCANNING
(3D)
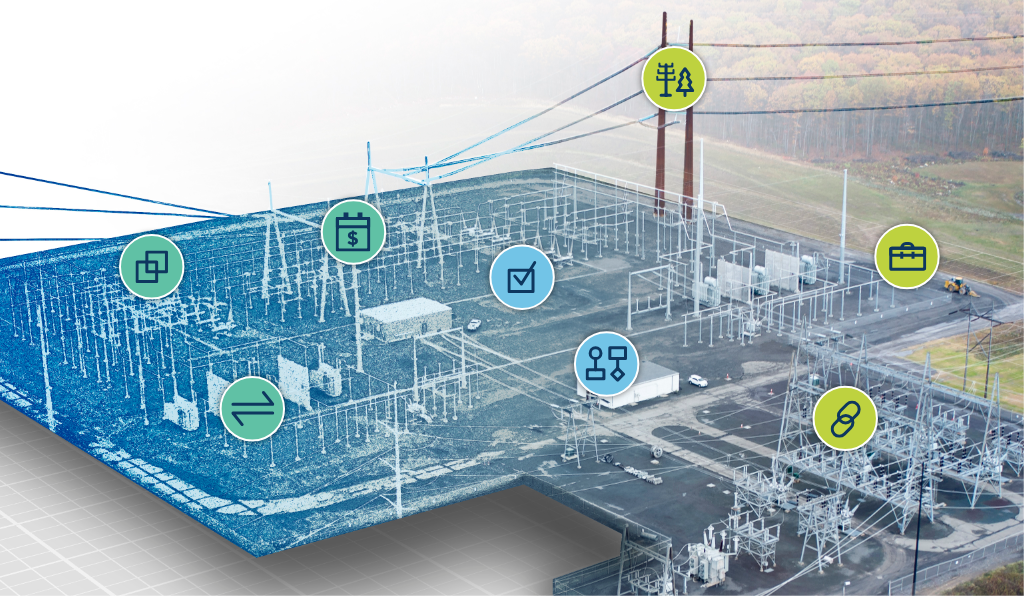
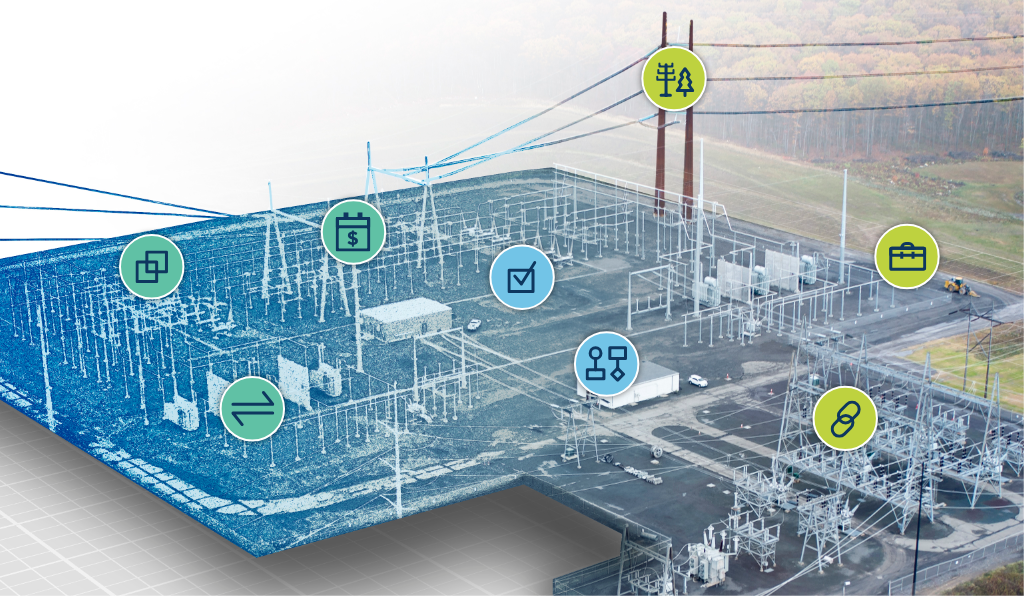
One benefit is its ability to provide the latest 3D information on existing site conditions using both 3D scans and design models. This makes it easier to guide planning decisions with highly accurate as-built information.
A digital twin is well-equipped with advanced tools and technology to monitor asset health, quickly identifying equipment that needs to be repaired or replaced, often enabling the use of predictive and condition-based techniques.
Digital twin technologies reduce the need for site visits to a generation plant or substation, saving time and money. If a site visit is required, leveraging real-time and other system and asset data from a digital twin will enhance personnel safety and site visit efficiency.
Knowing the explicit nature of an asset or process provides highly accurate system models. This is an invaluable aid in filling in any missing information or incomplete documentation.
Utilities that regularly conduct 3D scans of high-voltage transmission lines and other outdoor mission-critical assets can track and identify vegetation and other issues to support trimming and maintenance programs.
Switching from 2D drawings to 3D design software fundamentally changes the way power systems are planned and designed. Design involves creating a digital 3D model that easily can be manipulated and updated.
Utilizing this technology for an end-to-end system can be highly valuable in identifying the source of power outages, helping to speed recovery and improve customer satisfaction.
With machine learning and artificial intelligence, it is possible to build an operational history that can be mined for trends and predict upcoming maintenance needs.
One benefit is its ability to provide the latest 3D information on existing site conditions using both 3D scans and design models. This makes it easier to guide planning decisions with highly accurate as-built information.
A digital twin is well-equipped with advanced tools and technology to monitor asset health, quickly identifying equipment that needs to be repaired or replaced, often enabling the use of predictive and condition-based techniques.
Digital twin technologies reduce the need for site visits to a generation plant or substation, saving time and money. If a site visit is required, leveraging real-time and other system and asset data from a digital twin will enhance personnel safety and site visit efficiency.
Knowing the explicit nature of an asset or process provides highly accurate system models. This is an invaluable aid in filling in any missing information or incomplete documentation.
Utilities that regularly conduct 3D scans of high-voltage transmission lines and other outdoor mission-critical assets can track and identify vegetation and other issues to support trimming and maintenance programs.
Switching from 2D drawings to 3D design software fundamentally changes the way power systems are planned and designed. Design involves creating a digital 3D model that easily can be manipulated and updated.
Utilizing this technology for an end-to-end system can be highly valuable in identifying the source of power outages, helping to speed recovery and improve customer satisfaction.
With machine learning and artificial intelligence, it is possible to build an operational history that can be mined for trends and predict upcoming maintenance needs.
Want More?
Many industries have already seen the revolutionary influence of digital twin-enabling technologies, such as 3D design, visualization and printing. Learn more about how the power industry can prepare for the evolution of what is possible here.