HOW THE FLOW SYSTEMS WORK
Though there are dozens of different types of flow batteries, only about 10-12 specific chemistries appear ready for commercial applications. All operate on the same basic principle of incorporating liquid electrolyte to function as a source of direct current (DC) electricity that runs through an inverter for conversion to alternative current (AC) power.
In a reduction oxidation (redox) flow battery, positive and negative electrolyte solutions are stored in separate tanks. When power is needed, pumps are used to circulate the fluids into a stack with electrodes separated by a thin membrane. This membrane permits ion exchange between the anolyte and catholyte to produce electricity. The power produced is dependent on the surface area of the electrodes, while the storage duration is a function of the electrolyte volume. For some technologies, the power and energy can be scaled independently, allowing for an easily customizable battery.
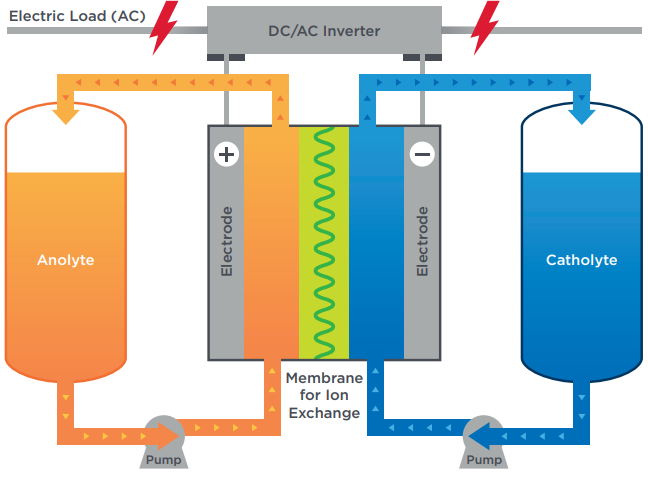
FIGURE 1: Diagram of flow battery process. Source: Summary of 2017 NASA Workshop on Assessment of Advanced Battery Technologies for Aerospace Applications.
In a hybrid flow battery, electroactive material is deposited on the surface of the electrode during the charge cycle and then dissolved back into the electrolyte solution during discharge. For hybrid technologies, the storage duration is a function of both the electrolyte volume and the electrode surface area. While most hybrid technologies can achieve durations of 6-12 hours, power and energy are not fully decoupled.
Flow batteries can be configured as a single tank — usually for smaller applications — or as a dual tank, usually on a larger footprint. The single-tank systems typically feature zinc or other metal batteries, while dual-tank systems are usually used for electrolyte composed of salt water, iron, vanadium or other minerals.
Flow battery system designs change depending on the application and project size. Behind-the-meter commercial systems are commonly kilowatt-scale packaged units that can fit into a typical utility room. For distribution applications in the 1-MW to 5-MW range, containerized and/or modular solutions exist with varying levels of scalability depending on the storage duration requirements. Utility-scale designs in development may have millions of gallons of electrolyte storage, so the industry is trending toward large quantities of stack modules headered together and piped to large, field-erected tanks.
Power stacks and balance of system components — like piping, pumps, seals, cooling systems and control instrumentation — require more routine maintenance than lithium-Ion configurations. However, if routine maintenance guidelines are followed, flow battery performance should not degrade within the project lifetime. When the O&M costs are compared to lithium-ion capacity augmentation costs required to offset performance degradation, flow battery annual costs are less expensive.