5 Equipment Options for Bottom Ash Conversion
Submerged Drag Chain Conveyor
An attractive option because of its low capital costs, the submerged drag chain conveyor system utilizes a wet impounded conveyor under the boiler. Falling ash is quenched by the water-filled upper trough of the submerged drag chain as it transitions in the hopper and is crushed before it’s pulled up a dewatering ramp.
“The submerged drag chain conveyor system is often considered a good option for a facility undergoing a retrofit, due to generally low costs and system reliability,” says Mike Roush, a project manager specializing in CCR at Burns & McDonnell.
While the system requires a large amount of room, the approach works for facilities looking to save time and money by having a simple and robust system to handle their ash.
Compact Submerged Conveyors
Under hopper compact submerged conveyors utilize much of the existing plant infrastructure but replace the wet sluice pipe with compact and fully submerged drag chain conveyors.
This approach works well for plants with limited space around the boiler bottom or those with an expected short life span. Additionally, under hopper compact submerged conveyors work for plants needing an option with limited operational disruption. Initial capital costs are relatively low and outages are generally limited, as the system builds on existing plant parts.
Remote Dewatering Systems
Remote dewatering systems function with the same basic technology as other systems, but conveyors are located away from the boiler. A completely closed-loop system, this approach avoids potential contamination of groundwater by constantly recycling and only discharging a small blowdown stream to maintain system chemistry.
This system works well for a plant with multiple boilers, or with boilers that have little space below the boiler for large equipment required by other alternatives. Outage time is typically short for this system, with dewatering systems constructed off-site.
Pneumatic Systems
Many utilities try to limit potential risk by preemptively converting systems to a completely dry solution. Dry solutions are only functional for pulverized coal boilers, as slagging and cyclone‑style boilers require a wetted bottom ash system to cool the ash.
A pneumatic system is a dry solution that limits risk by removing the potential exposure that ash might have with transport water. Ash from multiple boilers also could be conveyed to a single silo for a potentially more cost-effective solution, with less new infrastructure needed.
Dry Belt/Tray Conveyors
Dry belt tray conveyors offer another dry solution, one that avoids transport water with a belt system that transfers coal ash to a silo or bunker. Because of the high cost of installation, it is often appropriate for plants with a plan to operate for an extended period of time, as they will benefit from lower operation and maintenance costs.
These systems are commonly utilized in the European market, but only a few installations have been completed in the United States because of the typically higher cost. New regulations and more cost-effective system layouts, as well as a desire to remove water from the bottom ash equation, have pushed many plants in the U.S. to consider this technology for future conversions.
The RFID technology is inherently more efficient because you can capture data without expending nearly as much money and effort.
Nathan Sims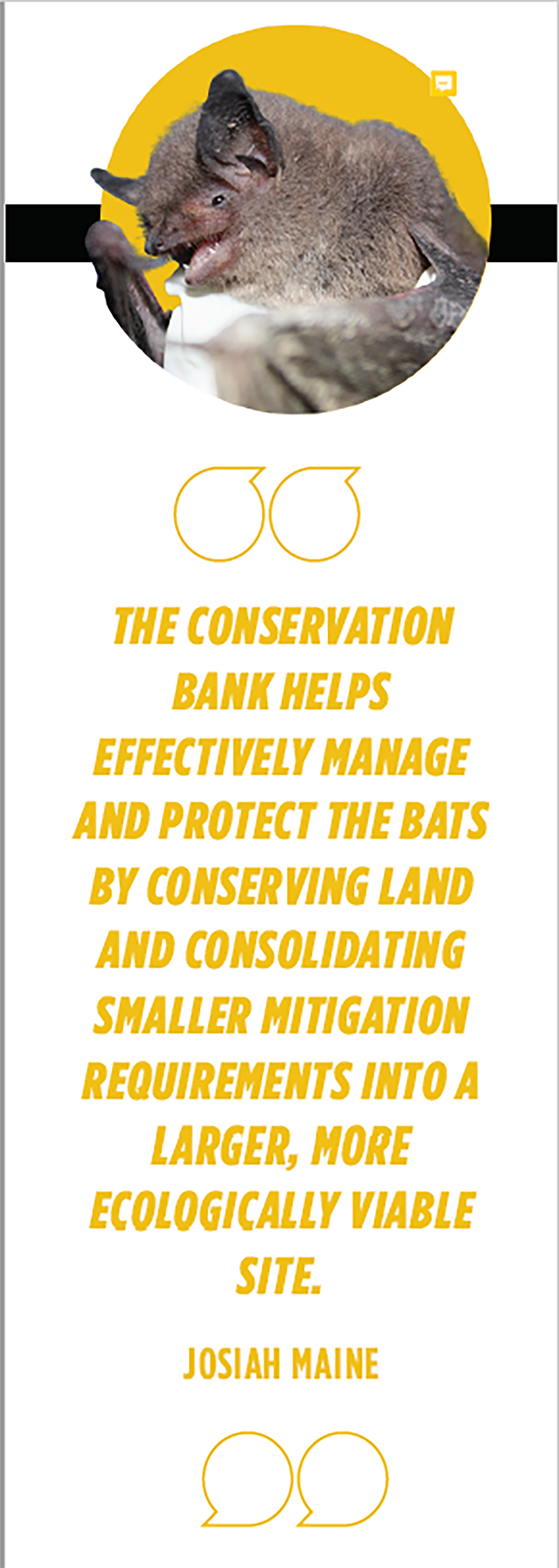
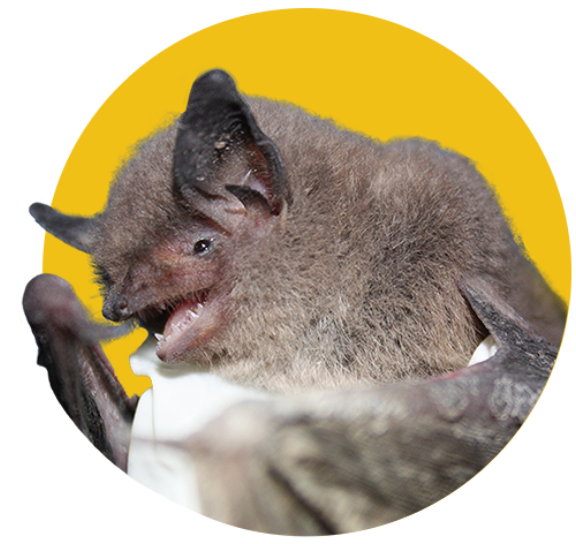

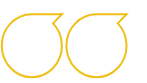
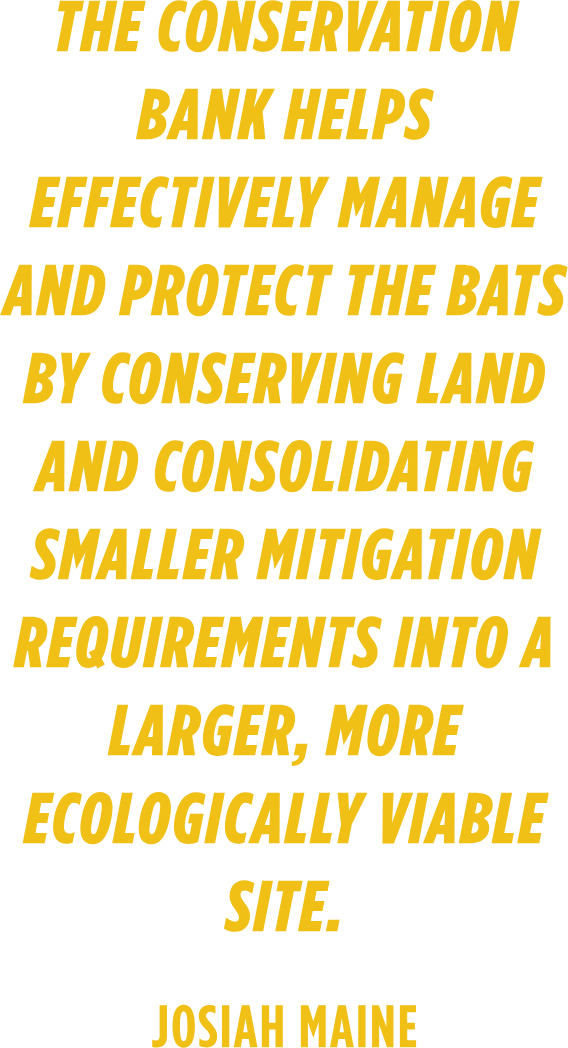
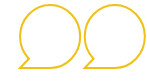
Want More?
Gain a deeper understanding of the latest technology in bottom ash conversion alternatives.
Read More